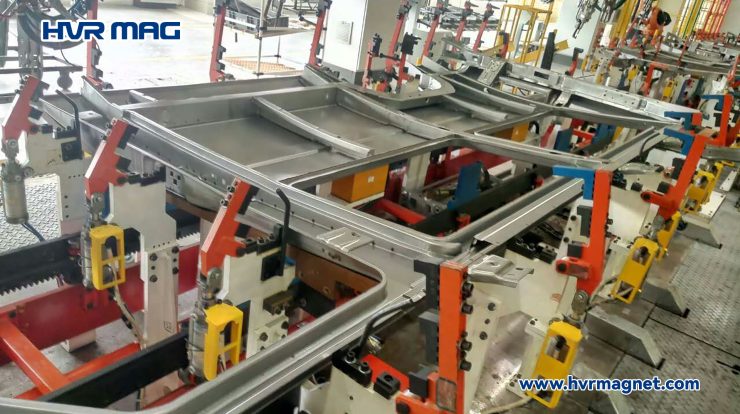
As the demand for electric vehicles (EVs) continues to grow, manufacturers are constantly seeking innovative solutions to streamline their production processes. One such solution is the use of electro permanent magnets as end-of-arm tools (EOATs) in EV manufacturing. These advanced magnets offer numerous advantages, including enhanced efficiency, improved precision, and increased versatility. In this article, we will explore the application of electro permanent magnets as EOATs in the manufacturing of electric vehicles.
Efficiency in Component Handling
Electro permanent magnets enable efficient handling of various components during the assembly of electric vehicles. Whether it’s lifting heavy battery packs or delicate electronic parts, these magnets provide a secure and reliable grip. The ability to switch the magnets on and off with short electrical pulses allows for quick attachment and detachment of components, drastically reducing production downtime. This efficient handling improves overall productivity and ensures a smooth assembly process.
Precise Positioning during Assembly
Achieving precise alignment during the assembly of EVs is crucial for ensuring optimal performance and safety. Electro permanent magnets enable accurate positioning of components with minimal effort. By utilizing the controllable magnetic force, the EOATs firmly hold the components in place, allowing precise alignment and preventing misalignment issues. This precision reduces the need for manual adjustments and rework, resulting in improved production efficiency and cost savings.
Versatility in Multi-Model Production
Manufacturers often produce multiple models of electric vehicles on the same assembly line, requiring adaptability and flexibility in tooling. Electro permanent magnets provide the versatility needed for rapidly switching between different components and vehicle models. With easy programmability, the magnets can be configured to fit various component shapes and sizes, allowing seamless transitions between different assembly processes. This adaptability saves time and resources, enabling manufacturers to respond effectively to changing market demands.
Enhanced Safety and Ergonomics
The use of electro permanent magnets contributes to a safer and more ergonomic working environment for assembly line operators. By eliminating the need for manual lifting, operators are less prone to strain or injuries associated with heavy component handling. Additionally, the secure grip provided by the magnets minimizes the risk of components slipping or dropping during assembly, reducing the potential for accidents and product damage.
Conclusion
In the realm of electric vehicle manufacturing, efficiency, precision, and adaptability are key factors determining success. Electro permanent magnets as end-of-arm tools offer a host of benefits that cater specifically to these requirements. Their efficient component handling, precise positioning, versatility in multi-model production, and improved safety make them invaluable assets for automakers seeking to optimize their production lines and meet the growing demand for electric vehicles. As the EV industry continues to evolve, the application of electro permanent magnets is set to play a vital role in driving innovation and advancement in electric vehicle manufacturing.
For more information, please contact HVR MAG at export@hvrmagnet.com