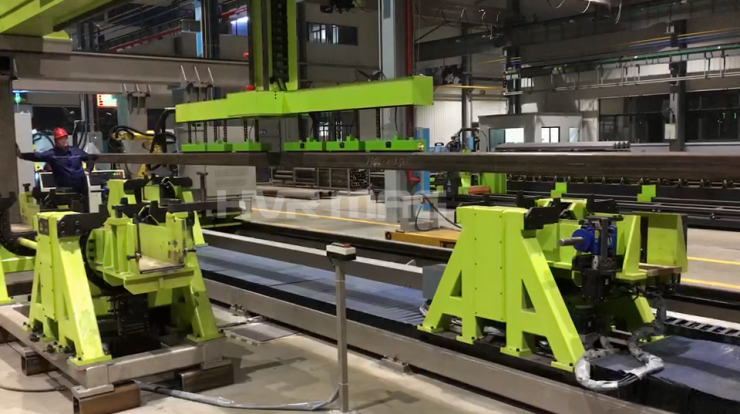
In mechanical processing, many are currently using manual or special machines for machine loading and unloading, which is very suitable in the case of a single product and low capacity. Still, with the progress and development of society, the use of manual or special machines for loading and unloading, the labor intensity is too great, easy to produce industrial accidents. And with the help of manual loading and unloading, product quality is not stable enough to meet the needs of high volume and high-quality production. The complex structure and inconvenient maintenance of special machines are not conducive to the automated assembly lines; they do not have the characteristics of flexible processing and are difficult to adapt to product changes, which is not conducive to the adjustment of product structure. Today we will talk about the need for automatic loading and unloading. (Take a truss robot as an example)
Automatic loading and unloading to achieve automation
1. Realisation of production automation
As far as the application of truss robots is concerned, it can realize automation in addition to mechanization. That is to say; when applied, it can sufficiently reduce the corresponding manual operation so that the CNC lathe can realize the automation.
2. Mechanisation
In terms of the application of the truss robot, we can use it in conjunction with the entire CNC lathe to achieve mechanized production and processing without the need for excessive manual operation. It is also clear that using robots makes applying CNC lathes very simple.
Automatic loading and unloading change the way of production to reduce enterprises’ dependence on the use of labor, reduce production costs and achieve sustainable development.
In the 21st century, vigorously carrying out technological innovation has become the core method of CNC automation industry development in the face of challenges and opportunities. Automatic loading and unloading robots have the characteristics of high-tech industries: high investment, high risk, high return, high technology, great difficulty, high potential, etc. Automatic loading and unloading robots are widely used in industrial industries such as electronics, electrical appliances, clocks and watches, hardware, auto parts, film, paper tape, and plastic.
As the level of modern industrial development continues to increase, the requirements for product quality and production efficiency continue to improve, and the mechanization of the production process continues to grow, loading and unloading robots are gradually being used in industrial production. We can widely use automatic loading and unloading robot technology in the CNC machining industry, improving production efficiency and saving more than 50% labor costs. It frees the operator from heavy, monotonous, and repetitive work.
Impact of automatic loading and unloading
The impact of automatic loading and unloading on the modern CNC manufacturing industry is vast, driving a new round of development of traditional industries. The market competitiveness is no less than the contemporary sunrise industry. Indeed, the days of intelligent production on paper are long gone, especially with the theme of “safety and energy efficiency,” and the work of automatic loading and unloading robots on assembly lines is undoubtedly more than enough to meet the needs of companies. Safety and quality are the two main drivers for developing automatic loading and unloading robots.
In the field of CNC machine tools, the use of automatic loading and unloading robots to replace manual loading and unloading work has become a trend, and automatic loading and unloading robots can meet the needs of industrial automation. By using loading and unloading robots and CNC machines to form a production line, the automation can improve labor productivity, reduce costs, and develop the production line into a flexible manufacturing system.
HVR magnetic grippers are in the CNC machine tool loading and unloading link to replace the manual work. The main objective is to adapt to large quantities, repetitive or workpiece weight is significant and the working environment with high temperature, dust, and other harsh conditions used. It has the characteristics of time tracking, stable product quality, reduced machine tool and tool losses, adjustable working tempo, smooth and reliable operation, easy maintenance, etc.
The truss robot can solve the automatic loading and unloading of CNC lathes. It has high efficiency and product quality stability; the simple structure is easier to maintain and can meet the production of different kinds of products. For the user, only limited adjustments need to be made, and it can quickly carry out product structure adjustments and expand production capacity, significantly reducing the labor intensity of industrial workers. Loading and unloading robots are involved in the processing and manufacturing of structural parts of machine tools to achieve automation, and machine tools serve the precision processing of robot reducers to improve the quality of the processing process and the efficiency of mass production, etc. There is excellent scope for integration and development.
If you want to know more about automatic loading and unloading magnetic grippers, please feel free to contact us.