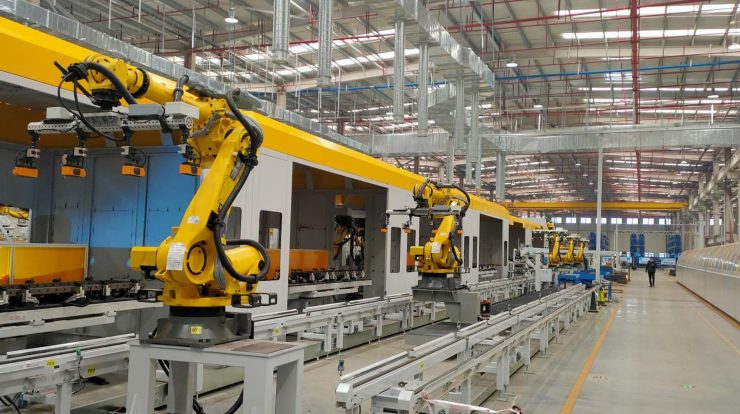
The development of CNC machines, high-speed, high-precision, composite, intelligent, open, parallel drive, network, extreme, and green, has become the trend and direction of the development of CNC machines.
1, high-speed
With the rapid development of automotive, national defense, aviation, aerospace, and other industries, as well as the application of new materials such as aluminum alloy, the high-speed requirements of CNC machine processing is increasingly high.
(1) spindle speed: machine tools using electric spindle (built-in spindle motor), the maximum spindle speed of 200000r/min.
(2) feed rate: in the resolution of 0.01μm, the machine can obtain the maximum feed rate of 240m / min from the complex surface of the precise processing.
(3) computing speed: the rapid development of microprocessors for the CNC system to the high-speed, high-precision direction to provide protection, the result of the CPU has developed to 32-bit and 64-bit CNC system, the frequency increased to several hundred megahertz, on the gigahertz. Due to the significant increase in computing speed, when the resolution of 0.1μm, 0.01μm can still obtain up to 24 ~ 240m/min feed rate.
(4) tool change speed: the current foreign advanced exchange time has generally been in about 1s, high has reached 0.5s. German Chiron company will be designed into a basket style with the spindle as the axis, the tool in the circumference of the arrangement, and the tool change time of only 0.9s.
2、High precision
CNC machine tool accuracy requirements are now not limited to static geometric accuracy; machine tool motion accuracy, thermal deformation, and monitoring and compensation of vibration are gaining more and more attention.
(1) improve CNC machining accuracy: the use of high-speed interpolation technology to achieve continuous feeding of tiny program segments so that CNC control unit refinement, and the use of high-resolution position detection device to improve the position detection accuracy (Japan has been developed with 106 pulses/revolution of the built-in position detector AC servo motor, its position detection accuracy can reach 0.01μm / pulse), position servo system using feed-forward control and non-linear control and other methods.
(2) Adopting error compensation technology: using backlash compensation, screw pitch error compensation, tool error compensation, and other technologies to compensate for the thermal deformation error and spatial error of the equipment. Research results show that applying comprehensive error compensation technology can reduce machining errors by 60% to 80%.
(3) The grid is used to check and improve the machining center’s motion trajectory accuracy. The machining accuracy of the machine tool is predicted through simulation to ensure its positioning accuracy and repeat positioning accuracy. So that its performance is stable in the long term and can complete various machining tasks under different operating conditions and ensure the machining quality of parts.
3, functional compounding
Composite machine tool is the meaning of a machine tool to achieve or as far as possible to complete from the blank to the finished product of a variety of elements of processing. Its structural characteristics can be divided into two types: process compound and process compound. Process compound machine tools such as boring, milling, and drilling compound – machining centers, turning and milling mix – turning centers, milling, boring, drilling and turning compound – compound machining centers, etc.; process compound machine tools such as multi-surface multi-axis joint processing of composite machine tools and dual-spindle turning centers, etc. The use of hybrid machine tools for processing reduces the workpiece loading and unloading, replacement, and adjustment of the additional time of the tool. And the error generated in the intermediate process improves the accuracy of parts processing, shortens the product manufacturing cycle, and improves production efficiency and the manufacturer’s market responsiveness, as opposed to the traditional process of scattered production methods have obvious advantages.
4, intelligent control.
To meet the development needs of manufacturing production flexibility and automation, the degree of brightness of CNC machine tools is constantly improving. It is reflected explicitly in the following aspects.
(1) process adaptive control technology: by monitoring the cutting force during processing, spindle and feed motor power, current, voltage, and other information, the use of traditional or modern algorithms for identification, to identify the tool force, wear, breakage state, and the stability of the machine tool processing state, and according to these states real-time adjustment of processing parameters (spindle speed, feed speed) and processing instructions, so that the equipment in the to improve machining accuracy, reduce surface roughness and improve the safety of equipment operation.
(2) Intelligent fault self-diagnosis and self-repair technology: based on existing fault information, modern intelligent methods are applied to achieve rapid and accurate fault location.
(3) intelligent fault playback and fault simulation technology: the ability to record a complete system of various information, the occurrence of multiple errors and accidents on CNC machine tools for playback and simulation, to determine the causes of errors, to find solutions to problems, to accumulate production experience.
(4) intelligent AC servo drive: can automatically identify the load and adjust the parameters of the intelligent servo system, including intelligent spindle AC drive and smart feed servo device. This kind of drive device can automatically identify the rotational inertia of the motor and load and automatically optimize and adjust the parameters of the control system so that the drive system can obtain the best operation.
(5) intelligent 4M CNC system: in the manufacturing process, processing, testing integration is to achieve rapid manufacturing, rapid detection, and rapid response to the practical way, the measurement (Measurement), modeling (Modelling), processing (Manufacturing), machine operation (Manipulator) four (i.e., 4M) integration in a system The 4Ms are used to share information and to promote the integration of measurement, modeling, machining, clamping, and operation.
Automation with HVR magnetic grippers
From energy-saving to high efficiency, HVR helps users to select equipment by studying their processed products, processes, production types, and quality requirements. And we recommend the most suitable magnetic grippers to help them make the most of their machines and process high-quality end products. Contact us if you are interested~