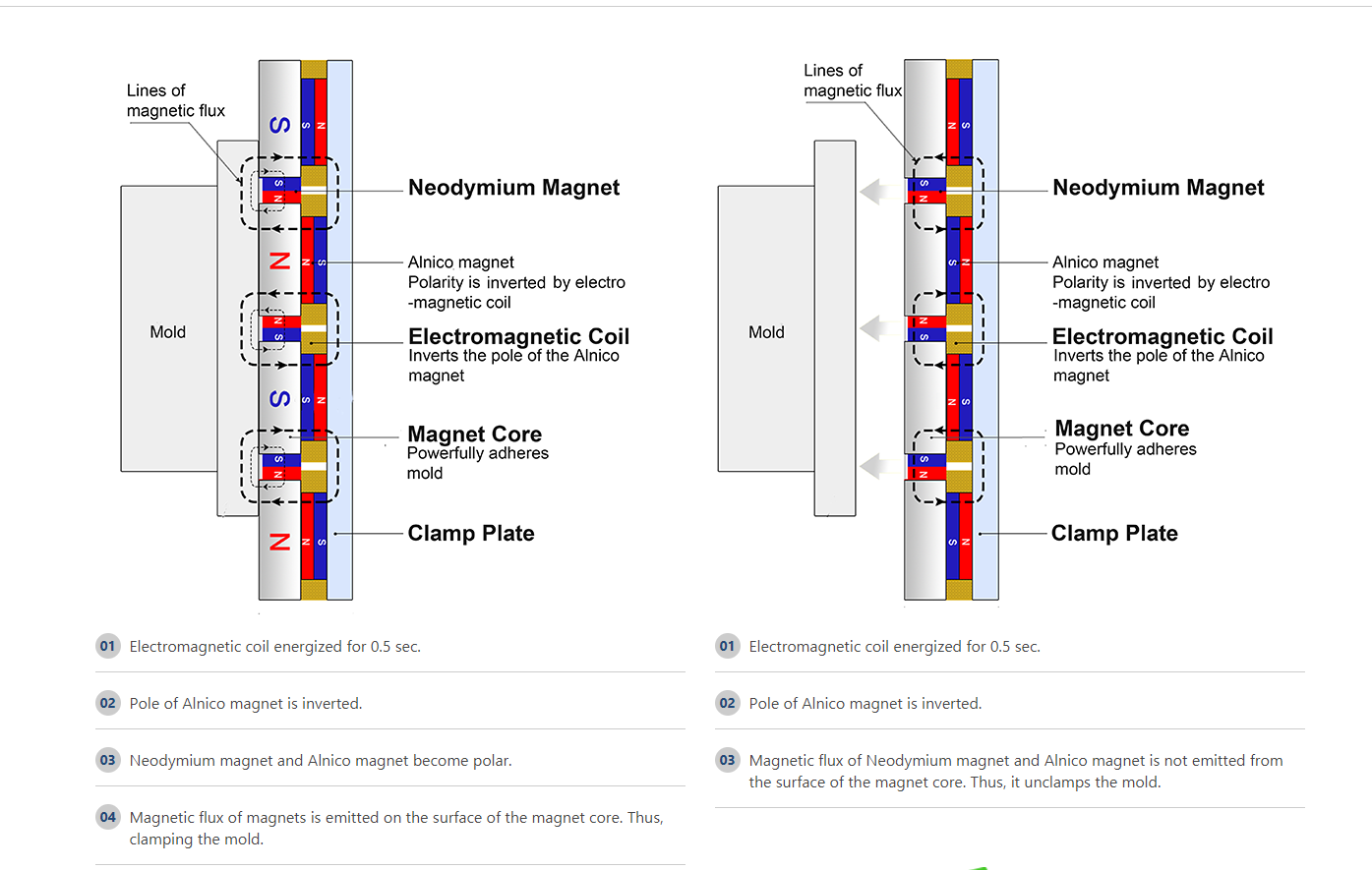
1.What Is Magnetic Clamping Technology?
The utilization of magnetic force to clamp on ferrous part to fixate it, for a type of working process. It could be permanent magnetic technology, electromagnetic, or electro-permanent magnetic technology. Usually it refers to two main kinds of applications: magnetic clamping for workholding, and magnetic clamp for mold change.
2.Magnetic Clamping System
It consists of the magnetic clamping device, either magnet chuck or magnetic clamping plate, and the electric control supplies for overall working process.
Magnetic mold clamping system, typically used in quick mold change for plastic injection molding machine.
Magnetic chuck & control system, generally applied in machining, like lathe, milling, surface grinding, and CNC machining center.
3.Magnetic Clamping Devices
Simply refers to the magnet clamp part, of the whole system.
Magnetic clamping plates, or otherwise called magnetic platens, mainly used for changing mold/die for plastic injection molding machines or punch presses.
Magnetic chuck, or magnetic work holding device, frequenly used machine tools in machining center.
4. Magnetic Workholding
Magnetic work holding has been around for over twenty years, but it is now becoming more commonplace for milling, turning, and grinding. Nowadays, machine tools and machining centers are designed for complex machining operations that can happen with a single set-up. Magnetic work holding offers an effective method of clamping production parts, as well as flexibility to accommodate families of parts, in such operations.
How It Works
Workpieces can be placed flat onto magnetic chucks and five sides of the workpiece can be easily accessed. The magnetic clamping force is evenly applied across the entire workpiece, thereby successfully reducing vibrations.
With magnetic chucks, the workpiece forms half of the magnetic circuit. The chuck is the engine, while the part is what closes the magnetic circuit and creates the clamping force. But it is important to consider that different materials have different magnetic saturation levels, resulting in different maximum holding forces.
Magnetic chucks are capable of holding workpieces as well as (or in many cases better than) mechanical clamps. A further benefit, of course, is that there are no clamps in the way of the machining process.
The magnetic system of choice for milling machine and machining center applications is called an electro-permanent magnet. This new concept is a hybrid of electro-magnets and permanent magnets. Electro-permanent magnets are operated by placing the workpiece on the magnet and pushing a button to send anelectric current that actuates the magnet. A second jolt is applied to de-energize the magnet when the work is complete.
Like a permanent magnet, this system can remain clamping on the workpiece for as long as you want it to unless you switched it off by giving another electric pulse. Most importantly, it consumes no power in clamping state, making it ideal for machining applications.
Advantages of Magnetic Work Holding
Speed: A magnet offers the quickest set up of any system which leads to less machine downtime.
Flexibility: chucks can be used with any ferromagnetic work piece, regardless of shape or size.
Clamp Uniformity: A magnet is the only system that provides full surface clamp force, which reduces vibration and enhances quality. Magnets allow the machine to cut with less chatter, and thus faster, by holding the total contact area of a workpiece. In addition, the lack of clamps around the workpiece allows the machine to cut without stopping. Programming is simplified, and time required to reposition the clamps is eliminated.
Clamp Consistency: Magnetic clamping technology offers predictable and reliable clamp force. These chucks have a consistent clamping pressure since the magnets are either on or off. The workpiece is always held firmly, unlike mechanical clamps and vises that may waver in tightness.
Low Maintenance: A magnet requires little to no maintenance, since there are no moving parts, no threads to strip, and no oil to clean.
Energy Efficient: Electrical consumption is only required for a few seconds for activation and deactivation.
As a manufacturer of magnetic chucks, HVR MAG offers a variety of magnetic workholding devices for milling (extremely high holding forces for machining on machining centers), turning (low-deformation clamping of rings and fitting disks) and grinding applications.
Magnetic clamping technology is a powerful addition to any machine shop looking to maximize its capability. For more information about the applications & benefits of this technology or to inquire about implementing in your workshop, welcome to visit our website: www.hvrmagnet.com.