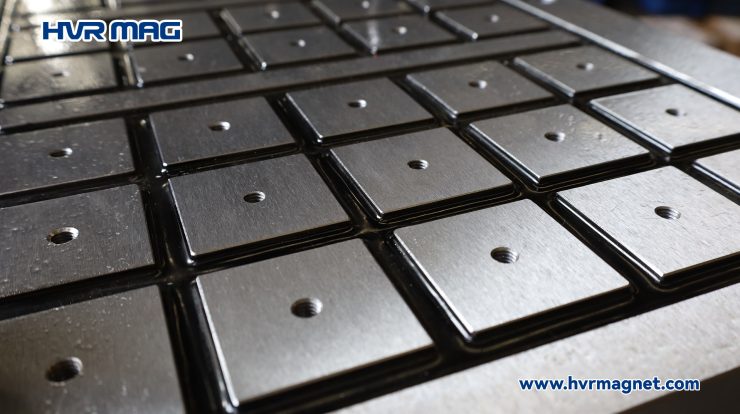
Powder metallurgy is a manufacturing process that utilizes metal powders to create intricate components with excellent mechanical properties. One critical aspect of powder metallurgy is the sintering process, where the compacted metal powder is subjected to elevated temperatures to achieve solidification and bonding. To facilitate this process efficiently and safely, electro permanent magnetic chucks have emerged as an innovative solution. This article delves into the benefits and applications of electro permanent magnetic chucks in powder metallurgy sintering.
Quick Mold Changeovers
Traditional toggle clamping chucks often require time-consuming manual adjustments and physical contact with hot molds during mold changeovers. Electro permanent magnetic chucks revolutionize this process by enabling rapid mold switching. The electrically controlled magnetic field allows for effortless and swift clamping and releasing of molds, thereby reducing downtime and enhancing overall production efficiency.
Worker Safety
Powder metallurgy sintering involves working with high temperatures that can pose safety risks to workers. Electro permanent magnetic chucks provide a safer working environment by reducing the working time in high temperature. This significantly reduces the risk of burns or other heat-related injuries.
Heat-Resistant Construction
Sintering processes involve extreme temperatures, which necessitate chucks capable of withstanding such conditions without deformation or loss of clamping force. Electro permanent magnetic chucks are constructed using specialized heat-resisting materials, coupling with water cooling system. These effectively endure the high temperatures encountered during sintering, ensuring consistent performance and longevity of the chucks.
Enhanced Flexibility and Versatility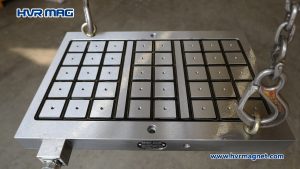
Electro permanent magnetic chucks offer tremendous flexibility and versatility in powder metallurgy sintering applications. They can securely hold molds of various shapes and sizes, accommodating the specific requirements of different component designs. The magnetic field distribution can be precisely controlled, allowing for optimal clamping force and uniform pressure distribution. This level of adaptability ensures high-quality and consistent sintering results across different production runs.
Improved Productivity
By streamlining the mold changeover process and reducing the time spent on manual adjustments, electro permanent magnetic chucks significantly enhance productivity in powder metallurgy sintering. The quick and efficient switching between molds minimizes downtime, allowing for uninterrupted production. This, coupled with the remote operation and superior heat resistance, translates to increased output, improved manufacturing cycle times, and ultimately, higher overall productivity.
Conclusion
Electro permanent magnetic chucks have emerged as an advanced solution in powder metallurgy sintering processes, offering numerous advantages over traditional clamping methods. Their ability to facilitate quick mold changeovers, enhance worker safety, provide heat-resistant construction, and offer flexibility and versatility highlight their importance in modern manufacturing. As the demand for efficient and safe powder metallurgy sintering continues to rise, the utilization of electro permanent magnetic chucks is poised to play a pivotal role in optimizing production processes and delivering high-quality components.
For more information, please contact HVR MAG at export@hvrmagnet.com