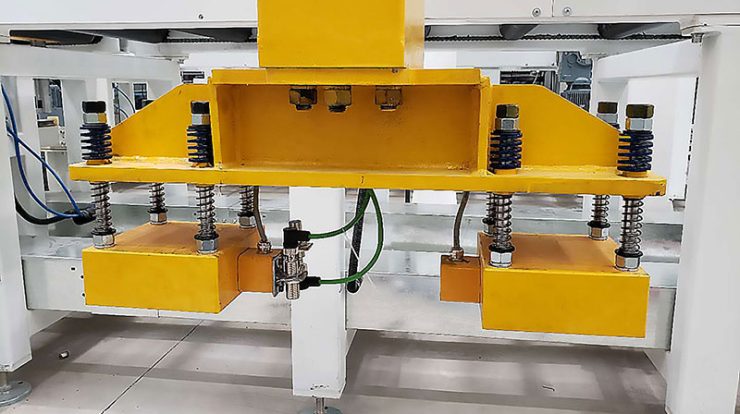
Industrial automation is a common aspiration in today’s manufacturing industry. Achieving industrial automation requires intelligent data management. But even more important is the availability of tools that can automate production. Both the industrial robot and its end effectors are important in this respect. HVR MAG offers you the most efficient magnetic end effectors.
How can magnetic end effectors help you automate your production? I will show you through this case. The factory in this case is located in Guangdong Province. Its products mainly include trailer parts such as semi-trailer axles, outriggers, suspension systems, saddles, drawbars and other trailer components. In their workshops, most of the production materials to be handled are steel. Magnetic gripper therefore work well here. Below is a before and after comparison of the use of magnetic grippers on two production lines at this company.
1. Loading and unloading of thin sheets
Before the use of magnetic end effectors, each time a thin steel plate was processed for loading, it was carried by wire rope or clamps. This required workers to fix the steel plates manually, which was time consuming and labour intensive. This line requires at least 4 people to load and unload the thin steel sheets. It is capable of handling 500 steel sheets per day. But the thin steel sheets are often deformed and worn due to the construction of the wire rope and clamps. On several occasions, safety accidents occurred because the steel plates were not fixed in place.
HVR MAG designed a set of magnetic end effectors in conjunction with the traversing robot. The machine automatically loads and unloads the steel plates. This means that the workers no longer have to fix the steel plates manually. They can now handle 1500 plates per day, which is three times more productive than before. The multi-point magnetic end effector avoids deformation of thin steel plates. And it doesn’t leave scratches. It is made of electro-permanent magnets. So it has two characteristics: the magnetism doesn’t get lost when the power is turned off, and it doesn’t heat up.
2.Steel tube handling
Handling steel tubes is more labour intensive than handling thin sheet. At least 6 workers are needed to load and unload the pipes. These tubes weigh 200-300 kg. Before using magnetic end effectors, they used straps and wire ropes to lift square and round tubes. They can handle about 400 tubes a day.
This line has also been converted from manual operation to a traversing robot and magnetic end effectors. Thanks to the powerful magnetic suction force of up to 16 kg per square centimetre of the electric permanent magnet, only one magnet is required. After the upgrade, this line can process approximately 1,500 tubes per day.
In short, the magnetic end effectors can directly pick up the steel without any manual intervention. Robotic trusses and magnetic grippers are much more powerful than humans. What is very tedious for humans is a piece of cake for automated production tools. That’s what industrial automation can do for manufacturing: make workers’ jobs easier and more productive.
If you are looking for an automated steel handling solution, HVR MAG can help. Feel free to contact us at:export@hvrmagnet.com