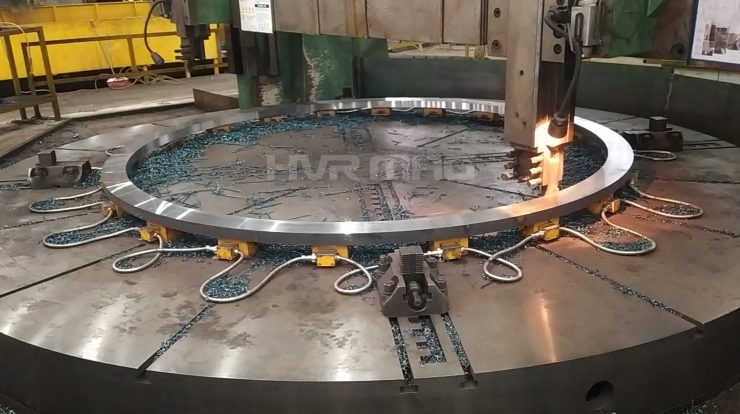
With the development of technology, the complexity of machining parts and processing accuracy is constantly improving, the requirements for processing speed are also getting higher and higher, and the application of advanced machining equipment such as magnetic chucks is becoming more and more popular.
In the past, parts processing was generally used vise, pressure plates, and other ways of clamping fixed. Parts clamping is cumbersome, some features need multiple clamping to complete processing, and clamping is difficult in the right place, affecting the accuracy of parts processing, resulting in scrap and other problems. The application of magnetic chucks can reduce the clamping time, reduce the number of times of clamping, and improve efficiency.
Electro-permanent magnetic chucks, now widely used magnetic jigs, can significantly improve steel clamping efficiency.
With a high-performance rare earth material NdFeB as the core, the HVR electro-permanent magnetic chuck uses a short pulse of current, thus changing the magnetic system of NdFeB inside the chuck to achieve the clamping and release of the workpiece being machined. The magnetic chucks are suitable for machining methods such as turning, grinding, milling and boring.
Turning
The workpiece is rotated, and the turning tool is moved in a straight or curved line. Turning is generally carried out on a lathe to machine the internal and external cylindrical surfaces, end faces, conical surfaces, shaped surfaces, and threads of the workpiece.
Turning accuracy is generally IT8~IT7, and surface roughness is 1.6~0.8μm.
(1) Rough turning strives to use considerable depth of cut and large feed to improve turning efficiency without reducing the cutting speed. Still, the machining accuracy can only reach IT11, and the surface roughness is Rα20~10μm.
(2) Semi-finishing and finishing turning as far as possible using high speed and small feed and depth of cut, machining accuracy up to IT10 ~ IT7, the surface roughness of Rα10 ~ 0.16μm.
(3) in the high precision lathe with delicate repair diamond turning tool high-speed precision non-ferrous metal parts, can make the processing accuracy of IT7 ~ IT5, the surface roughness of Rα0.04 ~ 0.01μm, this kind of turning called “mirror turning.”
Turning has strong adaptability to the workpiece’s structure, material, and production batch and is widely used. In addition to turning various kinds of steel, cast iron, and non-ferrous metals, it can also turn non-metals such as glass and steel.
Grinding
Grinding removes excess material from a workpiece with abrasives and tools and is widely used in the machinery manufacturing industry.
Grinding is usually used for semi-finishing and finishing, with an accuracy of IT8 to IT5 or even higher and a surface roughness of 1.25 to 0.16μm.
1)Precision grinding surface roughness is 0.16~0.04μm.
2) Ultra-precision grinding surface roughness is 0.04~0.01μm.
3) Mirror grinding surface roughness up to 0.01μm or less.
Grinding can process many materials, both available structural materials such as cast iron, carbon steel, and alloy steel, and difficult-to-cut materials such as hardened steel with high hardness.
Milling
Milling is a highly efficient method of cutting workpieces using a rotating multi-edge tool. It is suitable for machining flat surfaces, grooves, various shaped surfaces (e.g., splines, gears, and threads), and special-shaped surfaces of molds. According to the direction of the main movement during milling and the rule of feed to the workpiece is the same or opposite, it is divided into down milling and reverse milling.
The machining accuracy of milling can generally reach IT8~IT7, and the surface roughness is 6.3~1.6μm.
(1) Rough milling machining accuracy IT11~IT13, surface roughness 5~20μm.
(2) Machining accuracy IT8~IT11 in semi-finish milling, surface roughness 2.5~10μm.
(3) Finishing milling accuracy IT16~IT8, surface roughness 0.63~5μm.
Boring
Boring is a cutting process to enlarge the inside diameter of a hole or other circular contour with a tool. Its application generally ranges from semi-rough machining to finishing, and the tool used is usually a single-edged dull tool (called a boring bar).
1) Boring accuracy for steel materials is generally up to IT9~IT7, with a surface roughness of 2.5~0.16μm.
(2) Precision boring accuracy can reach IT7~IT6 with a surface roughness of 0.63~0.08μm.
Whether turning, grinding, milling, or boring, magnetic chucks can be used.
HVR has rich experience in electro-permanent magnetic chucks. Whether you work at the shipbuilding or metal fabrication plant, we have the right lifting magnet. Contact us today!